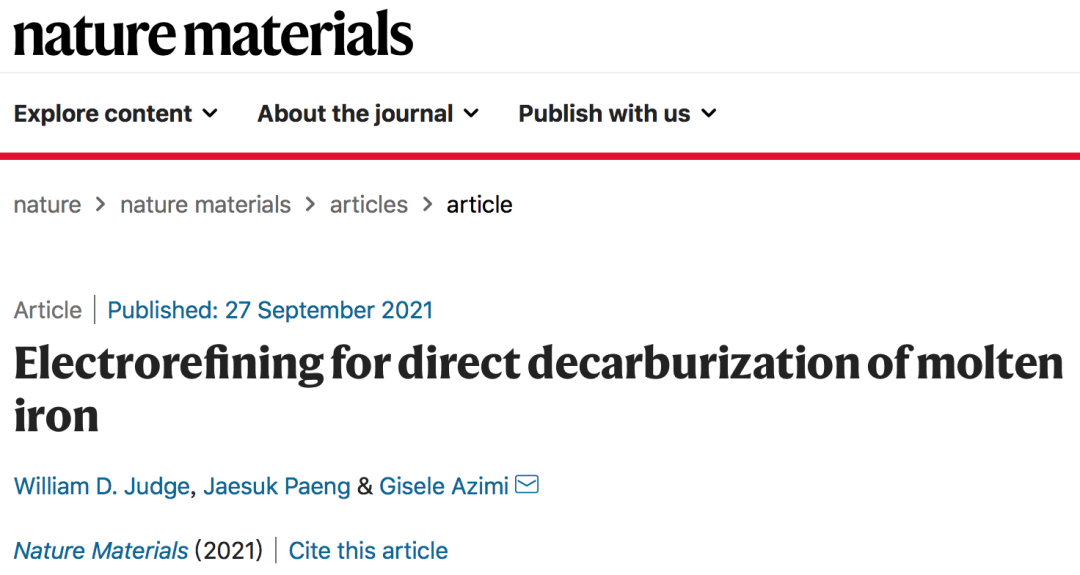
全球資源消耗量現在每年達到驚人的 900 億噸,這使得對環境的長期可持續發展面臨嚴峻挑戰。大多數原始材料的提取和制造過程都是能源密集型,會排放出大量溫室氣體。因此,材料再利用和回收利用是可持續發展的關鍵戰略。事實上,再利用和回收有助于人們實現循環經濟,但這一領域仍缺乏技術創新。在商品金屬中,鋼鐵的回收尤為重要。目前,全世界每年生產大約19億噸粗鋼,煉鋼占到了所有人為二氧化碳(CO2)排放量的約 7% 。大多數 CO2來自鋼廠初級鋼鐵生產的直接排放,其中每噸鋼約排放2.1-2.6 噸 CO2。同時,在小型鋼廠中使用電弧爐 (EAF) 回收廢鋼每噸鋼僅排放 0.4-1.0 噸CO2,大部分 CO2是來自發電的間接排放。 因此,在達到由循環維持的閉環時,CO2排放量將大幅減少。然而,這一結果取決于再生鋼的質量是否滿足需求。更高質量的鋼一直是鋼鐵消費行業所追求的目標。為了實現循環經濟,二次煉鋼必須嚴格控制碳等元素,將低價值的廢鋼轉化為高價值鋼。為了滿足材料要求,EAF生產的鐵水通常需要在幾個反應堆中進行處理,需要通過氬氧脫碳、真空罐脫氣或再循環脫氣進行精煉,才能將碳脫除到較低的水平。雖然這些技術可以脫碳,但它們是間歇過程,消耗試劑,金屬會流失到爐渣中。另一個問題是原料的可變性。廢鐵的成分差別很大,EAF中通常含有一些直接還原的鐵,其碳含量高達4%。因此,需要新技術來處理各種原料,以較少的試劑生產高價值的產品。在許多方面,電化學精煉技術能夠很好地克服傳統技術的局限性。當反應在熱力學上不利時,施加電勢就會迫使反應繼續進行。此外,電力成本相對便宜,EAF小型鋼廠已經建成了電力基礎設施。然而,迄今為止,電化學精煉的重點還是在碳飽和鐵(鐵水,由綜合工廠中高爐生產)和反應機制上,未實現工業應用。尚不存在用于EAF小型鋼廠、脫碳或下游低碳鋼生產的電精煉工藝。基于此,加拿大多倫多大學Prof. Gisele Azimi報道了開發了一種電解精煉工藝,通過在鐵水和渣電解液之間施加電動勢,實現直接鐵水脫碳。在陽極極化時,爐渣中的氧化物陰離子直接排放到溶解在鐵水中的碳上,形成氣態一氧化碳。值得一提的是,這種電解精煉直接通過界面反應實現脫碳,與高度依賴于與溶解氧反應的傳統做法截然不同。此外,該技術僅需要低能量輸入且無需試劑,便可生產超低碳鋼并在陰極回收硅作為副產品。因此,這項技術有望滿足二次鋼廠未來的需求。在實際生產中,由于碳與氧的高親和性,且易于脫除的氣態產物一氧化碳,所以通常采用氧化來脫碳。工業轉爐一般使用氣態氧及其通過噴槍和風口吹出的稀釋混合物對鐵熔體進行脫碳。以這種方式,脫碳不僅在碰撞熱點處進行,而且還通過溶解在鐵中的氧間接進行。而與傳統完全不同的是,研究人員將煉鋼爐渣中的氧化物離子電化學放電作為鐵水脫碳的途徑。其不依賴于中性氧原子或分子與碳的化學反應,而是表明脫碳可以通過釋放氧化物離子來形成一氧化碳而無需氧氣中間體。為了研究熔渣中鐵液的電精煉,研究人員設計了一個電化學池(圖1a),并對其進行了概念性操作。采用二硼化鋯作為惰性電極連接鐵液,從而使得鐵液自由極化。對電極在電解槽內垂直定向,并從中心偏移,使得電解槽進行不間斷的氣體演化和可視化觀察(圖1b)。脫碳是通過各種鐵碳中間合金在充當電解液的氧化物基渣中的陽極極化進行的。該電解槽電位為脫碳反應向極低碳水平進行提供了熱力學驅動力。圖1b顯示,確實觀察到在陽極極化時從鐵水-碳電極中釋放出的氣體。在恒流調制下運行,研究人員隨著時間的推移跟蹤廢氣成分,并在極化開始時檢測到一氧化碳的釋放。工作電極(圖1d)證實發生了脫碳。電解精煉后,碳濃度從母合金中的 3.78 wt% 降低到 0.84 wt%,電流效率高達 76%。精煉后鐵中的總氧含量僅為 0.0054 wt%,表明鋼具有高清潔度,并突出了氧化物直接排放在碳上而不是進入鐵熔池的趨勢。在電解精煉過程中,通過在反電極處發生相等且相反的反應,在電池中保持電中性,反電極在這里充當陰極。在設計的爐渣中含有二氧化硅和其他更具電負性的金屬氧化物,以利于硅的回收,研究人員利用這個機會在對電極處回收金屬硅作為副產品,方便其在煉鋼廠中使用。反電極的表征證實了金屬硅的沉積,其與鉬基板形成合金(圖1e)。考慮到已經確認了碳的去除、一氧化碳氣體的產生和金屬硅的沉積,研究人員提出了以下總體電池反應:[C] + 1/2(SiO2) = CO(g) + 1/2Si(l) (1)這些結果顯示,通過在鐵水和爐渣之間施加電動勢,可以實現鐵水脫碳。有理由相信該過程是直接氧化碳,并且可以通過優化電流或電位調制來進一步提高效率。圖1 實驗證明電解精煉在1600 °C下對含3.78 wt%碳的鐵水可進行直接脫碳根據反應物和產物的消耗和生產,研究人員確定了整個電池反應是按照反應(1)進行的;然而,并沒有獲得關于陽極半反應路徑((O2?)+ [C] =CO(g) +2e?)的信息。研究人員進行了詳細的電化學研究,以闡明反應機理并測量其動力學參數。對含不同量碳的合金和純鐵進行了電化學阻抗譜分析(圖2a)。結果顯示,碳大大降低了電荷轉移電阻并增加了合金的界面電容。通過繪制相互電荷轉移電阻與合金中碳的化學活性來測試交換電流的依賴性(圖2c),在寬的組成范圍和接近二分之一的特征斜率上的定量關系表明,碳直接參與剩余電位下的電位決定反應。進一步的,研究人員探索了陽極極化過程中脫碳是如何進行的,得到了穩態極化曲線(圖2b)和Tafel交換電流和合金中碳活性之間的關系(圖2c)。在選定的半對數圖上的線性關系遵循Tafel’s方程,表明在這些選定區域內發生了電荷轉移控制下的反應。在1650和1700 ℃的極化曲線驗證了Tafel’s方程預測的斜率隨溫度升高而變陡,交換電流的高激活能(273±2 kJmol-1)與活化控制一致。以Tafel行為為特征的反應代表了涉及碳的不同反應或步驟。在某些電流密度下,極化曲線偏離Tafel行為,表明發生了新的速率決定步驟,或者更有可能的是,傳質控制優先。研究人員總結了脫碳反應的可能方案(圖2e)。推導出了理論Tafel斜率,并為每種可能的反應方案、速率決定步驟和表面覆蓋率交換了當前反應順序(圖2f)。將實驗觀察結果與可能的速率確定步驟進行比較,發現只有圖2e 中的反應 (a)明顯匹配。因此,陽極極化期間的速率確定步驟對應于氧化物離子的初始放電:(O2?)+[C]=C(O?)ads+e? (3)研究人員分析了不同合金恒流電解精煉過程中的氣體瞬變(圖2d)。觀察到一氧化碳的釋放遵循準一級反應動力學,還觀察到表觀速率常數與電流無關,即使后者幾乎是電流的三倍。基于一氧化碳析出速率常數與電流的無關性,研究人員得出結論,脫碳是按照圖2e中的方案(I)進行的。因此,一氧化碳的解吸根據:圖2 電化學技術闡明了鐵水在1600 °C時的脫碳途徑研究人員進一步闡明了脫碳機理按照圖3中的示意圖進行。碳使析氧反應去極化,從而使氧化物離子的放電直接發生在碳上。脫碳通過一系列單電子轉移步驟進行,然后是一氧化碳的化學或物理解吸。在第一步中,氧化物陰離子在金屬-渣界面處直接排放到碳上,形成吸附中間體C(O-)ads。研究人員測量了該反應的動力學常數。在隨后的步驟中,來自氧化物離子的第二個電子被釋放以形成中性吸附中間體C(O)ads。最后,一氧化碳分子從界面物理或化學解吸并成核或加入現有氣泡。此外,圖3中還描繪了有助于補充界面處碳的電渦流混合現象。研究人員進一步探索了電解精煉的能力并對該技術進行了基準測試。如圖4a所示,碳濃度的降低伴隨著脫碳電流效率的相應降低。然而,電流效率從未達到零,證明熔融電精煉可以在任何碳濃度下進行。因此,本工作將碳含量僅為0.005 wt%的電精煉鐵引入到0.001 wt%以下,并將電精煉作為一種制備超低碳鋼的方法。雖然這里的電流效率只有1-2%,但由于電池電流低,電荷和能量損失很小。因此,可以通過優化電池電流或電位來提高電流效率。研究人員密切監測了熔渣中的總鐵含量。熔渣中的總鐵含量保持在較低水平,但略有上升,接近熱力學平衡(圖4b,c)。由于交換的電子未知,鐵在開路時自然溶解。檢測到了熔渣中的FeO和Fe2O3,它們形成了依賴于熔渣中局部電位梯度的復雜平衡。相反,通過考慮單位電荷通過的鐵損量,發現在低碳水平下鐵損量趨于增加。雖然對于較低的碳含量,每法拉第鐵的分數損失看起來很高,但實際上由于電池電流較小,其損失幅度較小。為了降低鐵損,通過改變晶胞極性,考察了其從精煉后的渣中電化學回收。作者將鐵水作為陰極,鐵從渣中沉積回來,其在渣中的濃度大大降低(圖4b)。因此,本工作能夠從渣中回收損失的鐵,提高了工藝的收率。在這里,作者通過電化學方法進行回收,證明了其在降低試劑成本方面的潛在的優勢。為了評估鋼的潔凈度,研究人員測量了鐵中的總氧,代表了鐵中溶解的氧和來自夾雜物的氧的總和。結果顯示,電精煉鐵雖然含碳量較低,但其總氧含量極低(圖4c)。此處的總氧很可能接近溶解氧,說明有較高的潔凈度。低于與碳的平衡溶解度極限的氧水平,進一步證明氧化物離子的放電直接發生在界面處的碳上,而不是它們進入鐵熔體。這與增加鋼氧化的常規脫碳工藝形成鮮明對比。1)提出了一種用于鐵水直接脫碳的電解精煉概念。當鐵水陽極極化時,熔渣電解液中的氧化物離子通過一系列單電子轉移步驟直接釋放到溶解在鐵中的碳上,然后脫附氣體一氧化碳。隨著一氧化碳從陽極釋放出來,有價值的冶金級硅在陰極處被回收,作為副產品用于鋼鐵廠。2)電精煉工藝適用于任何含碳量的鐵水,研究人員演示了超低碳鋼的生產。此外,電解精煉能耗低,不需要試劑,自混合,可以從爐渣中回收金屬。同時,除了滿足當前對高質量鋼材的需求外,研究人員還預計,由于工藝控制容易以及氣體、脫氧劑和耐火材料消耗較低,這可能會節省成本。3)除了作為一個獨立的過程運行外,電精煉還可以與現有技術結合使用,以加強精煉。研究人員設想,電爐精煉的主要應用是在EAF小型鋼廠回收鋼材,這些鋼廠擁有現有的電力基礎設施,可以生產高價值產品。通過提高回收鋼的質量,電解精煉有助于材料閉環,減少資源消耗,并減少煉鋼過程中的排放。Judge, W.D., Paeng, J. & Azimi, G. Electrorefining for direct decarburization of molten iron. Nat. Mater. (2021).
DOI:10.1038/s41563-021-01106-zhttps://doi.org/10.1038/s41563-021-01106-z