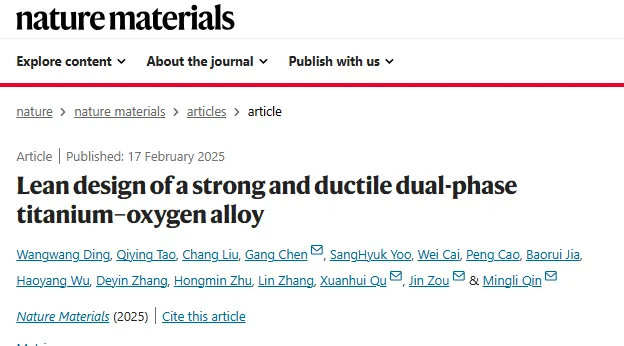
研究背景
鈦是具有優(yōu)異延展性、生物相容性和耐腐蝕性的材料,廣泛應(yīng)用于化學(xué)、石化、醫(yī)療和牙科等領(lǐng)域。與傳統(tǒng)的高強(qiáng)度合金材料相比,鈦具有較低到中等的強(qiáng)度,這限制了其在苛刻結(jié)構(gòu)應(yīng)用中的使用。雖然傳統(tǒng)的強(qiáng)化方法,如固溶體強(qiáng)化、沉淀硬化和工作硬化,能夠提高鈦的強(qiáng)度,但這些方法往往會犧牲其延展性,同時成本較高且能量消耗大。此外,傳統(tǒng)合金化方法還需要使用昂貴的合金元素,這進(jìn)一步限制了鈦材料的廣泛應(yīng)用。因此,如何在不犧牲延展性的前提下提高鈦的強(qiáng)度,一直是鈦材料研究中的重大挑戰(zhàn)。鑒于此,北京科技大學(xué)秦明禮、曲選輝、陳剛以及澳大利亞昆士蘭大學(xué)鄒進(jìn)等人合作在“Nature Materials”期刊上發(fā)表了題為“Lean design of a strong and ductile dual-phase titanium–oxygen alloy”的最新論文。該研究通過設(shè)計(jì)和制備一種鈦氧合金,成功實(shí)現(xiàn)了強(qiáng)度與延展性兼?zhèn)涞拟伈牧稀Q芯咳藛T采用激光粉末床熔化(PBF-LB/M)技術(shù),通過精確控制粉末的氧化物層厚度,成功在六方密堆積鈦基體中嵌入了相干的納米級面心立方鈦相。該創(chuàng)新方法不僅顯著提高了鈦材料的強(qiáng)度,同時保持了良好的延展性。實(shí)驗(yàn)結(jié)果表明,Ti–0.67 wt% O合金的拉伸強(qiáng)度為1,119.3±29.2 MPa,延展性為23.3±1.9%。這一成果突破了傳統(tǒng)鈦材料強(qiáng)化方法的局限性,為開發(fā)高性能、成本效益高且可持續(xù)的鈦合金材料提供了新的技術(shù)路徑。
研究亮點(diǎn)
(1)實(shí)驗(yàn)首次通過激光粉末床熔化(PBF-LB/M)技術(shù),將相干的納米級面心立方(fcc)鈦相嵌入六方密堆積(hcp)鈦基體中,成功制備了雙相鈦氧合金(Ti–0.67 wt% O)。該合金展示了顯著的強(qiáng)度提升,同時保持了較高的延展性。(2)實(shí)驗(yàn)通過精心設(shè)計(jì)的粉末,其中表面具有約30 nm厚的富氧層,使得氧含量大幅增加,氧化物層的厚度顯著高于傳統(tǒng)鈦粉末。通過PBF-LB/M技術(shù)的快速冷卻,該氧層與基體相互作用,有效地促進(jìn)了fcc鈦相的形成。 (3)實(shí)驗(yàn)結(jié)果表明,所制備的Ti–0.67O合金在拉伸測試中表現(xiàn)出優(yōu)異的機(jī)械性能,最終拉伸強(qiáng)度為1,119.3±29.2 MPa,延展性為23.3±1.9%。這種增強(qiáng)的力學(xué)性能為鈦合金的應(yīng)用提供了新的思路,特別是在結(jié)構(gòu)材料中具有潛力。
圖文解讀
圖1.定制設(shè)計(jì)的高氧鈦粉及其熱處理前后以及打印成型試樣的微觀結(jié)構(gòu)。圖2.打印態(tài)雙相Ti-0.67O合金的微觀結(jié)構(gòu)。圖3.直接打印的雙相Ti-0.67O合金的機(jī)械性能。圖4.拉伸后打印態(tài)雙相Ti-0.67O合金的微觀結(jié)構(gòu)。
結(jié)論展望
總之,本文展示了一種簡化合金設(shè)計(jì)策略,通過將相干的納米級面心立方鈦相(fcc Ti)引入六方密堆積鈦基體(hcp Ti),其中層狀fcc Ti相的體積分?jǐn)?shù)為23.5±4.0 vol.%,其平均寬度為79±39 nm,平均長度為1,044±346 nm。我們的方法在鈦合金開發(fā)中具有顯著的可持續(xù)性和成本效益優(yōu)勢,消除了對昂貴合金元素(如釩和鉬)的需求。該方法使用低成本的氫化–去氫化鈦粉末,其成本至少比氣體噴霧法制備的鈦粉便宜50%以上。此外,打印得到的Ti–0.67O合金在高達(dá)700°C的溫度下展現(xiàn)出優(yōu)異的熱穩(wěn)定性,并在700°C時表現(xiàn)出強(qiáng)度和延展性的顯著結(jié)合。這一特性在航空航天和化學(xué)加工等廣泛應(yīng)用中具有重要前景。本研究為設(shè)計(jì)經(jīng)濟(jì)且可持續(xù)的高性能簡化鈦合金開辟了新的方向。Ding, W., Tao, Q., Liu, C. et al. Lean design of a strong and ductile dual-phase titanium–oxygen alloy. Nat. Mater. (2025). https://doi.org/10.1038/s41563-025-02118-9